Additive manufacturing
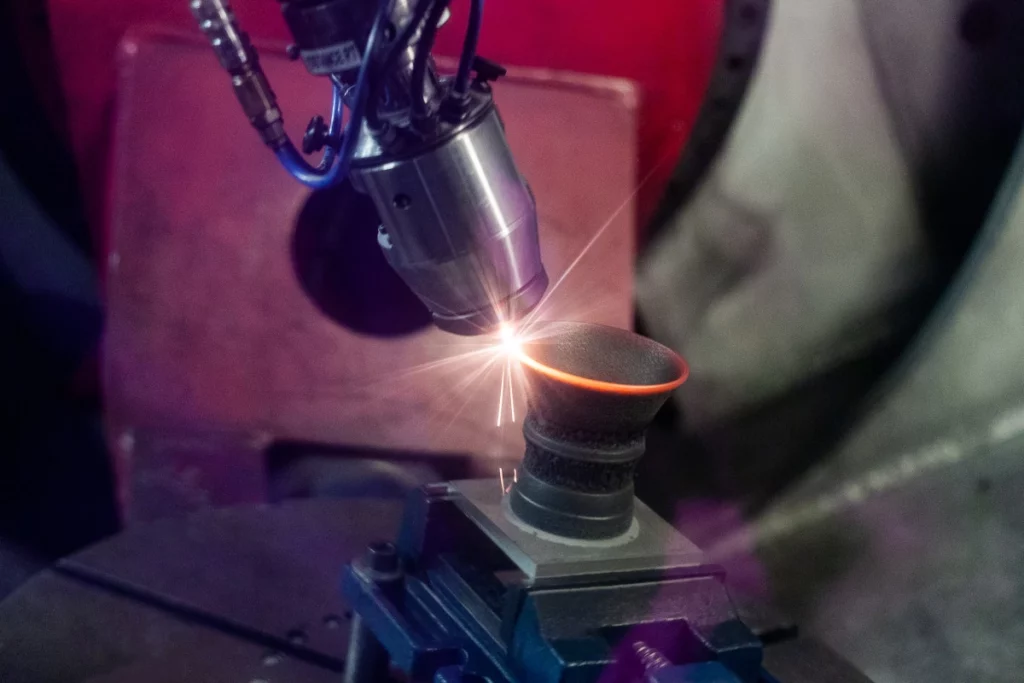
Presentation
Additive manufacturing subcontracting: entrust your production to us
DOUBLE CŒUR masters the production of large, complex parts right the first time for modern industries.
Call on our team of specialized engineers and technicians to support you in your projects.
Large-scale wire and/or powder metal additive manufacturing: the industrial laser revolution.
Our equipment
Our DED additive manufacturing machine
Additive manufacturing, also known as WLAM DED (Wire Laser Additive Manufacturing by Direct Energy Deposition), is a manufacturing process in which successive layers of material are melted together.
The result is a 3D printout of the functional object. We produce a part directly from its digital representation, giving engineers free rein to be creative!
DED BeAM additive manufacturing machine
2 AMFREE inside robots
Turning device diameter 2.5 m
1300 cm3/hour
Complex parts
Large parts
Short production lead times
Steel, aluminum, nickel-based or titanium alloys
Technology
Quality, speed and flexibility for your custom parts
Thanks to metal additive manufacturing, we can produce even highly complex parts, while reducing costs and production times, and increasing quality compared with conventional industrial manufacturing. You’ll no longer have to wait for long lead times to get your parts prototyped or manufactured.
The flexibility of our additive manufacturing machines enables us to produce a large number of parts entirely tailored to our customers’ particular needs. Our filler materials (powder or wire) are vacuum-packed, corrosion-protected and insulated from each other. We can manufacture from steel, aluminum, nickel or titanium base materials.
Read more
Additive manufacturing meets every challenge
A controlled process with ‘AMFREE inside’: total supervision and traceability
Laser additive manufacturing with wire is a technique that enables 3D objects or shapes to be produced using CAM software, which generates the manufacturing trajectory. The object is cut into layers, which are successively deposited after the laser beam has simultaneously fused the substrate and the wire. The relative movement between the laser processing head and the wire feeder in relation to the substrate is performed by a computer-controlled robotic arm.
This process makes it possible to produce large parts with minimal thermal distortion. The use of a laser beam offers better control of heat input than the arc-wire additive manufacturing process, which limits the risk of thermal distortion.
With AMFREE technology, all parameters are under control, such as laser power, material deposit speed and part temperature at each stage of construction. All these parameters are servo-controlled, guaranteeing both traceability and the quality of the part produced. DOUBLE COEUR is thus able to supply large objects as close as possible to the targeted geometries.
Thermomechanical simulation
DED WLAM additive manufacturing is faced with an economic imperative: to manufacture large-scale functional parts that conform to specifications the first time (metallurgical quality, geometry, etc.). DOUBLE COEUR carries out thermomechanical simulation to ensure that materials are properly controlled and failures anticipated. Engineers simulate thermal propagation in an object to be manufactured, then deduce its mechanical behavior by calculating deformations and stresses.
Our modeling team retrieves the CAD of the part to be manufactured and integrates its thermal characteristics (thermal conductivity of the material, mass heat capacity, coefficient of thermal expansion). Then, using our calculation software, it simulates thermal propagation in the part by applying thermal changes representative of the environment. Once the state has stabilized, we identify the thermal field generated and then estimate the deformation of the part that will create stresses and lead to breakage.
We can simulate all possible temperature ranges and deduce the best process parameters to minimize deformation. What’s more, we can virtually test different designs to determine which will behave more reliably than others. In this way, DOUBLE COEUR limits the number of laser machine trials required to get the part right the first time.
Prototypes
Production of custom parts (prototypes, qualification parts, blanks, etc.)
Preseries
Manufacture of parts or sub-assemblies (ramp-up, load shedding, production safety, etc.)
Productions
Series production to confirm the robustness of a new process (qualification, robustness, single reference, small series, etc.).
Application areas
All industrial fields
Aeronautics
Spatial
Nuclear
Energy
Automotive
Rail
Contact
A team of laser experts at your service
Contact us today to benefit from expert advice, impeccable service quality and an industrial partnership tailored to your needs.
Together, we can make your most ambitious projects a reality.